GLOW: New technology for safer measurement of oil shipment purity
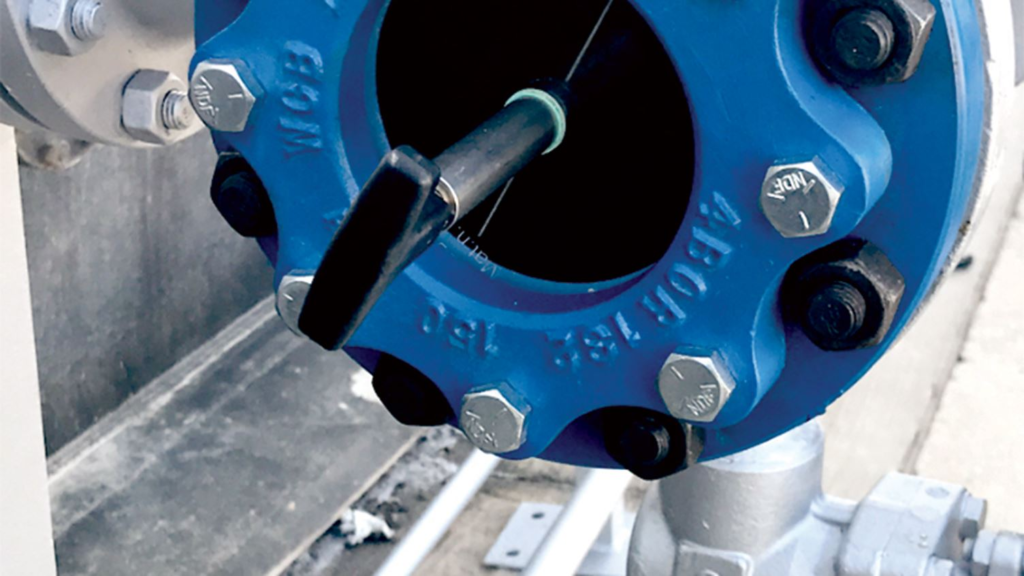
Before a single barrel of crude oil is shipped to an awaiting ship at Saudi Aramco’s terminal in Ras Tanura, operators must certify the purity of the crude oil in their tanks. A new technology, called ground level optical water cut (GLOW), allows to check the water content of a crude oil shipment in a safe and timely manner.
Traditional methods used by the industry for verifying the water content of crude oil have not changed much over the decades. In most oil terminals around the world, an operator is sent to the top of a crude oil tank to lower a depth gauge coated with chemicals that identify how much water rests. Strong winds or rains have been a constant challenge, preventing operators from the risk of climbing tanks for hours or even days — a costly delay for both the company and its customers.
The GLOW innovation allows operators to verify the water content of a crude oil shipment in a safe and timely manner, without putting operators at risk. It utilizes an optical glass and a series of pipes in a closed looping system, extended into the tank. The system provides the same accuracy with much less risk of exposure to heights and toxic gases. This will reduce the total man-hours by more than 80% over the conventional method.
Safety as an inspiration
“The main reason for this technology is safety for the operator,” said Shaker M. Al Mahrous, manager of Saudi Aramco’s Terminal Operations. “The GLOW device will disrupt the conventional way of performing water cut activity and will reset the industrial standards. This solution eliminates the main cause of incidents in the industry, which is falling from heights.
“And yet, this solution still allows us to provide the verification that our customers need. GLOW allows us to see what water is in the tank in an instant, without the risk to our personnel,” he added.
Developed and tested entirely within the company by Fahad S. Alnamasi, an engineer, the genius of the GLOW solution is its simplicity. A series of seven pipes are installed in seven different elevations from the bottom of the tank. When the operator needs to know the water content, he just needs to open a valve to let the fluid from a certain pipe flow into the header where the contents can be viewed through an optical glass.
“I wanted to make the innovation as simple as possible because the cost is cheap,” said Alnamasi. “The sight glass is $1,000. If you include the pipes, the total cost is about $5,000. This compares with millions for higher technology solutions. A small investment with huge returns; enhancing safety, avoiding ships delays, improving quality, and saving costs.”