SABIC TO SHOWCASE AT MD&M WEST 2024 SPECIALTY MATERIALS FOR LEADING MEDICAL DEVICE CHALLENGES
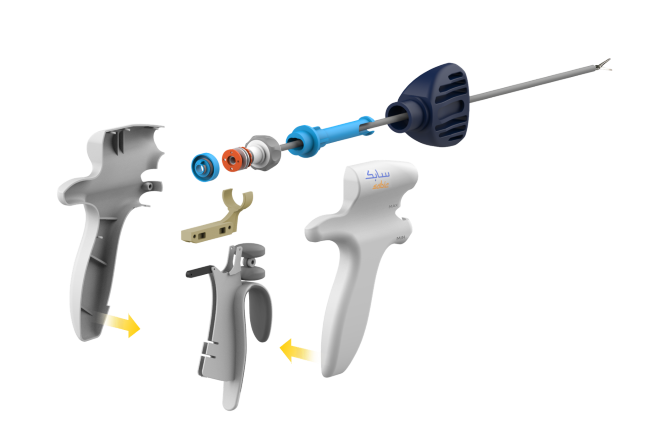
SABIC, a global leader in the chemical industry, will feature new and existing material solutions for potential use in critical medical devices through the company’s exhibition and two presentations at MD&M West 2024 (Booth #3287). The company will spotlight specialty engineered thermoplastic materials that can help the device industry address pressing issues, including withstanding increasingly harsh healthcare disinfectants; providing effective lubrication without the use of polytetrafluoroethylene (PTFE); and finding alternatives to EtO sterilization in the face of upcoming U.S. Environmental Protection Agency (EPA) regulations. SABIC’s first presentation will focus on new material technology that is well suited for wear and friction applications and the second will cover material solutions for medical device sterilization.
“SABIC’s Specialties business is eager to showcase at MD&M West 2024 our latest material technologies to help improve device performance, durability, compliance and sustainability,” said Maureen MacDonald-Stein, director, Portfolio Strategy and Marketing, SABIC’s Specialties Business. “As a longstanding preferred supplier to the industry, we deliver more than 100 innovative products backed by a robust Healthcare Product Policy and comprehensive support services. We are committed to helping our customers stay ahead of rapidly changing requirements, technologies and global regulations.”
COPING WITH HEALTHCARE CHEMICALS
The frequent application of highly aggressive disinfectants can cause environmental stress cracking (ESC) in plastic medical device housings and components. Degradation of the material could interfere with patient care or result in costly premature device failure and warranty claims. SABIC’s ULTEM™ HU resin series and LNP™ ELCRES™ CRX copolymer resins deliver best-in-class chemical resistance, helping to mitigate or prevent ESC and extend the useful life of devices.
AN ALTERNATIVE TO PTFE
SABIC’s specialty compounds can also help solve restrictions or bans on per- and polyfluoroalkyl substances (PFAS). Internally lubricated LNP LUBRILOY™ compounds, featuring a patented olefinic additive, provide an attractive alternative to materials lubricated with PTFE, a type of PFAS. The portfolio is being expanded with new base resins.
To provide technical data on LNP LUBRILOY compounds, Ed Williams, senior product manager, LNP Compounds, will give a presentation on Tuesday, February 6, at 12:30 p.m. PST in the MD&M West Design Alley. The presentation is titled “Solving thermoplastic wear and friction problems in medical devices without intentionally added PFAS.”
ANTICIPATING ETO STERILIZATION RESTRICTIONS
Another device challenge is the ability to withstand multiple sterilization methods and repeated sterilization cycles. Anticipated EPA restrictions on EtO sterilization emissions are prompting demand for versatile thermoplastics – like ULTEM HU resins – which are compatible with the most common sterilization methods including steam autoclave and vapor hydrogen peroxide (VHP) sterilization, and gamma/E-beam radiation, to name a few – and can withstand repeated sterilization cycles.
At the show, Paul Nugent, SABIC’s senior business manager, will give a presentation, titled “How thermoplastic material selection impacts durability and sterilization of medical devices.” His presentation will take place on Wednesday, February 7 at 3:30 p.m. PST in Design Alley. Nugent will discuss trends such as stricter regulations and the strong demand for sustainability and extending the life of parts, which affect the selection of materials for medical devices. He will also explain how the properties of ULTEM HU resins align with these trends and can surpass those of competitive materials.
EXPANDING PRODUCT PORTFOLIO
Also, at MD&M West, SABIC will feature materials that can add value to connected devices (ULTEM resins, LNP FARADEX™ compounds and LNP ELCRES™ DMX copolymers) and structural applications (ULTEM resins and reinforced LNP THERMOCOMP™ compounds), and advance sustainability with bio-circular or chemically upcycled content.
SABIC’s medical-grade products are backed by its Healthcare Product Policy, which verifies these materials meet global safety standards, are covered by an FDA Drug or Device Master File and are subject to formula lock and a stringent change management process.