SPECIALIZED SABIC® PP-UMS FOAM RESIN CAN HELP REDUCE VEHICLE EMISSIONS AND INCREASE RECYCLABILITY
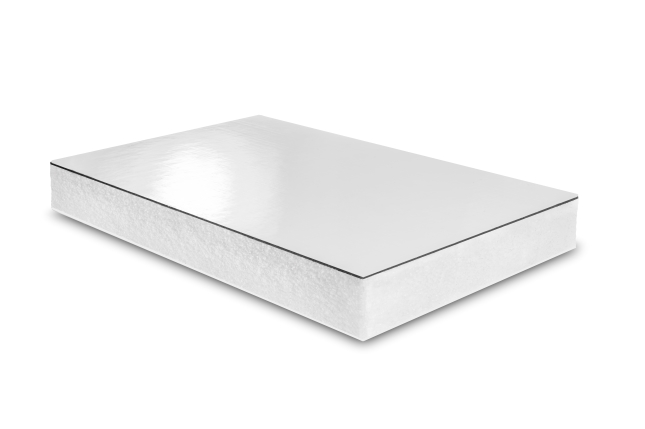
- SABIC is exhibiting at NPE2024 two transportation applications that demonstrate the exceptional lightweighting, processing and sustainability features of SABIC® PP-UMS foam resin.
- A recreational vehicle (RV) floor sandwich panel with an extruded foam core and a blow-molded foam air duct showcase different processing approaches and value propositions.
- SABIC® PP-UMS foam resin delivers exceptionally high melt strength for outstanding foamability and compliance with VDA 278 emission regulations.
- SABIC® PP-UMS foam resin enables production of low-density foams via the foam extrusion process.
SABIC, a global leader in the chemical industry, is spotlighting two diverse transportation applications that demonstrate the potential benefits of SABIC® PP-UMS (Polypropylene – Ultra Melt Strength) foam resin at NPE2024 (Booth #S19005). This distinctive material features high melt strength for outstanding foamability and enables the extrusion of PP foams with very low density, excellent impact resistance and compliance with VDA 278 emissions regulations. SABIC® PP-UMS foam resin’s processing versatility allows PP foams, subject to user testing, to be used in structural cores for sandwich panels in delivery vans, trucks and recreational vehicles (RVs), and to provide structural and insulative properties in blow-molded air ducts. Examples of these applications, on display at the SABIC booth, illustrate the suitability of this foam resin for broad use in transportation components that can benefit from significant weight reduction and potential cost optimization.
“This distinctive foam resin with exceptional melt strength enables the extrusion of PP foam with very low density, which can help the transportation industry advance lightweighting goals by replacing heavier material combinations ranging from metal and wood to solid polymers,” said Amanda Roble, director, Advanced Consumer Solutions, SABIC. “But SABIC PP-UMS foam resin does even more. Its purity and cleanliness address the most stringent automotive emissions regulations, while its processing flexibility and blendability make it adaptable to many different applications. We look forward to working with the transportation value chain to develop new and innovative foam solutions.”
Foam Cores Well Suited for Sandwich Panels
The PP foam produced with SABIC® PP-UMS foam resin can function as a strong, insulative core material for sandwich panels in trucks, delivery vans and RVs, replacing metal, wood and competitive foams. Panels with PP foam cores produced from SABIC® PP-UMS resin can reduce weight and help lower carbon dioxide emissions.
The SABIC foam resin is typically combined with other PP materials to produce the foam core. Adding a glass fiber-reinforced PP face sheet results in a mono-material part that is easier to recycle than a mix of material types. Furthermore, foam produced with SABIC® PP-UMS foam resin can be thermally bonded to the PP face sheet, avoiding the need for adhesives.
Another advantage of the SABIC® PP-UMS foam resin-based panel is its impact resistance. In addition, panels using the SABIC foam resin can be repaired easily if damaged, and are durable because the foam resin does not react with water.
A sample composite PP sandwich panel from an RV floor, comprised of a glass fiber-reinforced PP face sheet and foam core, is on display at the SABIC booth.
Blow-molded Foam for Potential Use in Auto Air Duct
Blow-molded PP foam produced with SABIC® PP-UMS foam resin can be used in automotive air ducts to help reduce weight and simplify the mounting process in the vehicle. The SABIC® PP-UMS foam resin solution creates a mono-material part for easy recycling in existing waste systems. An air duct, approximately 60 inches long, is in commercial use and can be viewed at the SABIC booth.
Beside weight savings and recyclability, this air duct offers additional functionality, including insulation properties that can save energy and help extend the range of electrical vehicles. This inherent insulative capability and a smart design help manufacturers avoid the need to add insulation to the part. The results are additional savings on weight and cost (labor and material).
SABIC® PP-UMS foam resin is a new-generation, long chain branched PP material with a melt strength greater than 65 cN to enable very low foam densities (20 – 200 kg/m3). It offers a broad processing window using various methods: foam extrusion, foam injection molding, foam blow molding, particle foaming, and foam blown and cast film. SABIC supports its materials with the resources of the Foam Innovation Center in the Netherlands. The center provides leading-edge technologies and a platform for collaboration with customers and organizations across the foam industry value chain.